製品の開発・製造
ガラスの製造工程
板ガラスの製造工程は、環境への影響が大きいものの1つです。
AGCでは製造工程の中でエネルギー効率を上げる技術開発や燃料方式の変更等に取り組んでいます。
原材料
板ガラスの製造に使用される基本的な原材料は次のとおりです。
- ・ガラス原料:珪砂、ガラスカレット
- ・炭酸ナトリウム、ドロマイト、石灰石、硫酸ナトリウム、長石、高炉スラグなどの中間および改質材料
- ・酸化鉄等の金属化合物等の着色・コーティング剤
フロートプロセス
フロートガラスの製造では、原材料を混合し、炉で溶かして溶融ガラスを形成し、溶融スズの槽に注ぎます。炉は空気と天然ガスの燃焼を利用して原料を溶かします。ガラスが冷えて固まると、錫浴に浮かび、ガラスのリボンが形成されます。この時点で、スズ浴の最後または直後にガラスにコーティングを施すことができます。その後、ガラスリボンは徐冷ゾーンに移動し、ローラーで運ばれながら徐々に冷却され、シートに切断されます。
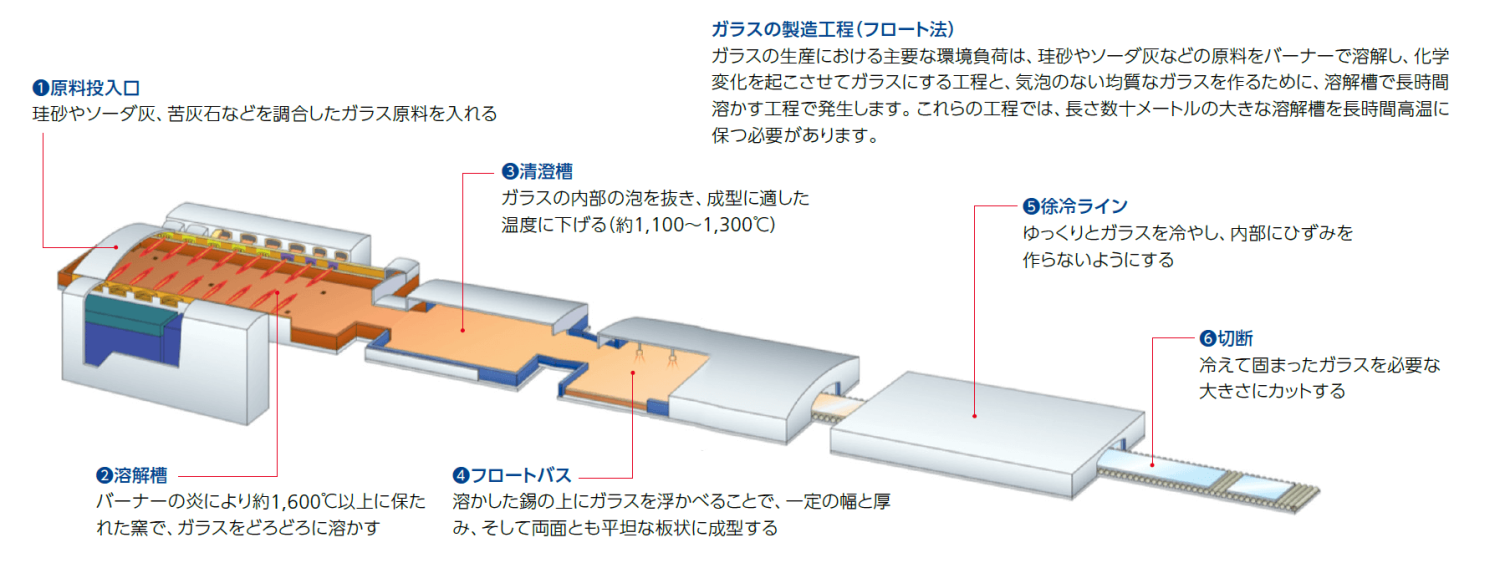
さらなる処理
ガラスが冷えた後、他の製品に加工することができます。例えば:
- ・ミラー用ガラスは塗装および銀メッキが可能
- ・建築用ガラス(建物、家具など)は、コーティング、複層ガラスの製造、強化、エナメル、塗装、ラミネート、エッチングなどを行うことができます。
製造時におけるGHG排出量削減に向けた取り組み
カレット(ガラス屑)の利用
製品製造時に発生するカレット(ガラス屑)をガラス原料として再投入して、再利用しています。
ガラス原料と混合して使用することで、珪砂、ソーダ灰などの天然資源の消費を削減できます。また、天然原料を溶融させるよりも、カレットを再投入することで消費エネルギーを減らすことができます。その為、カレットの利用促進はGHG排出量削減に大きく寄与します。
今後も、カレット消費量の増加を促進し、GHG排出量削減による気候変動対応、資源の有効活用による資源循環への貢献を進めていきます。
資源の有効利用
燃料転換
AGCグループではガラス溶解などに用いる重油を天然ガスに代替する燃料転換を一部の設備で導入しています。天然ガスは、重油に比べて燃焼時のCO2排出量を約20%削減できます。さらに、燃料起因のSOx(硫黄酸化物)の排出がほぼゼロとなるため、SOx排出量の低減も可能になります。
今後は、燃料転換に加え、酸素燃焼方式の導入、燃料使用量を低減する溶解用電気ブースターの導入、溶解熱源の電化といった様々な技術を組み合わせ、さらなる省エネを目指します。
また、AGCグループの断熱性が非常に高いセラミックス技術とガラス溶解技術とのコンビネーションにより、さらにエネルギー効率を高めていくことが期待されます。
省エネガラス製造技術
エネルギー効率の向上
全酸素燃焼
全酸素燃焼法は、燃料を酸素だけで燃焼させてガラスを生産する方式です。空気の約80%を占め、燃焼には必要のない窒素を加熱せずに済むため、エネルギー効率が高まります。
また、燃焼ガス中に窒素がほとんど含まれないことから、NOx(窒素酸化物)の発生を抑制する効果もあります。
アンモニア燃焼技術開発プロジェクト
AGCは、国立研究開発法人新エネルギー・産業技術総合開発機構(NEDO)の委託事業「工業炉における燃料アンモニアの燃焼技術開発」の委託先に採択されました。2021年12月末から2026年3月にかけて、大陽日酸株式会社、国立研究開発法人産業技術総合研究所、国立大学法人東北大学とともに共同開発を行っています。
AGC横浜テクニカルセンターの建築用ガラス製造設備にアンモニアと酸素の混焼バーナーを導入し、アンモニア燃焼技術の実証試験を行います。アンモニア燃焼におけるガラスや溶解炉を構成する材料への影響を評価するとともに、環境基準を満たすことのできるバーナーを開発し、ガラス溶解炉への本格導入を目指します。
実証試験を行うガラス溶解炉
ガラス溶解炉内部
ガラス輸送パレットのIoT化
ガラスの物流には特殊なパレットを使った高効率物流を行っています。このパレットに特殊な電波を発する素子を入れることにより位置情報を把握することを一部大型パレットで実用化しています。
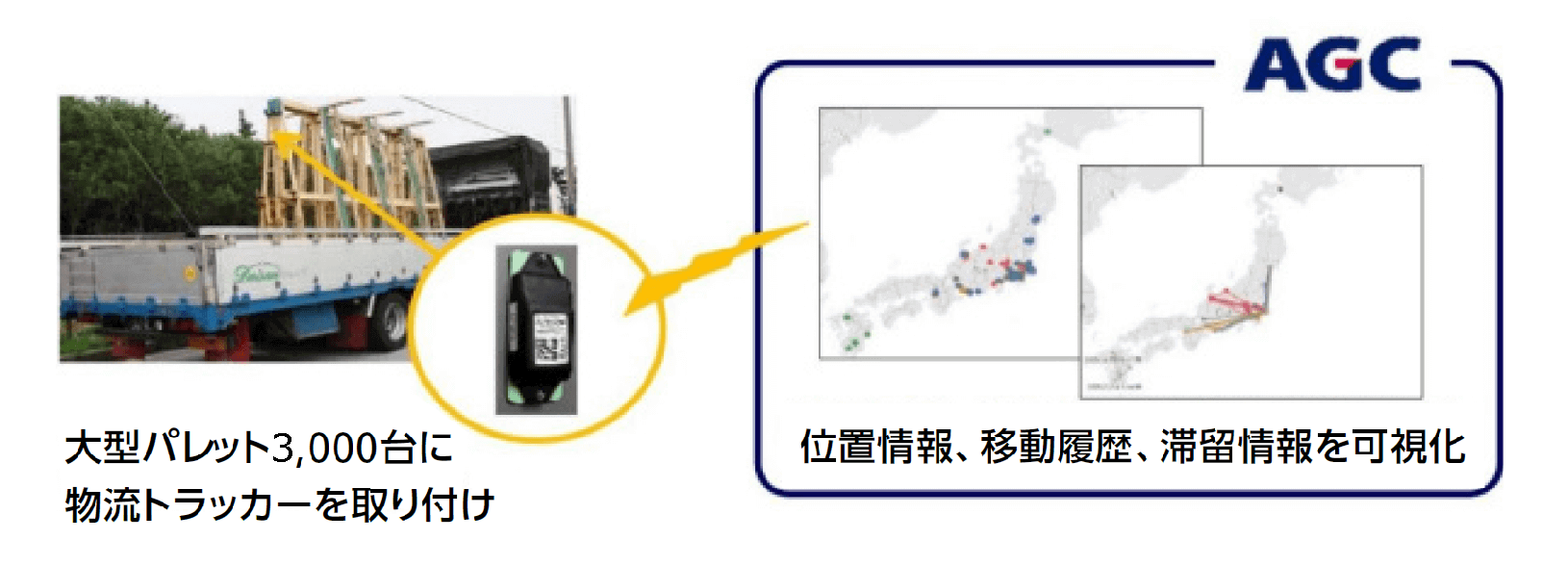